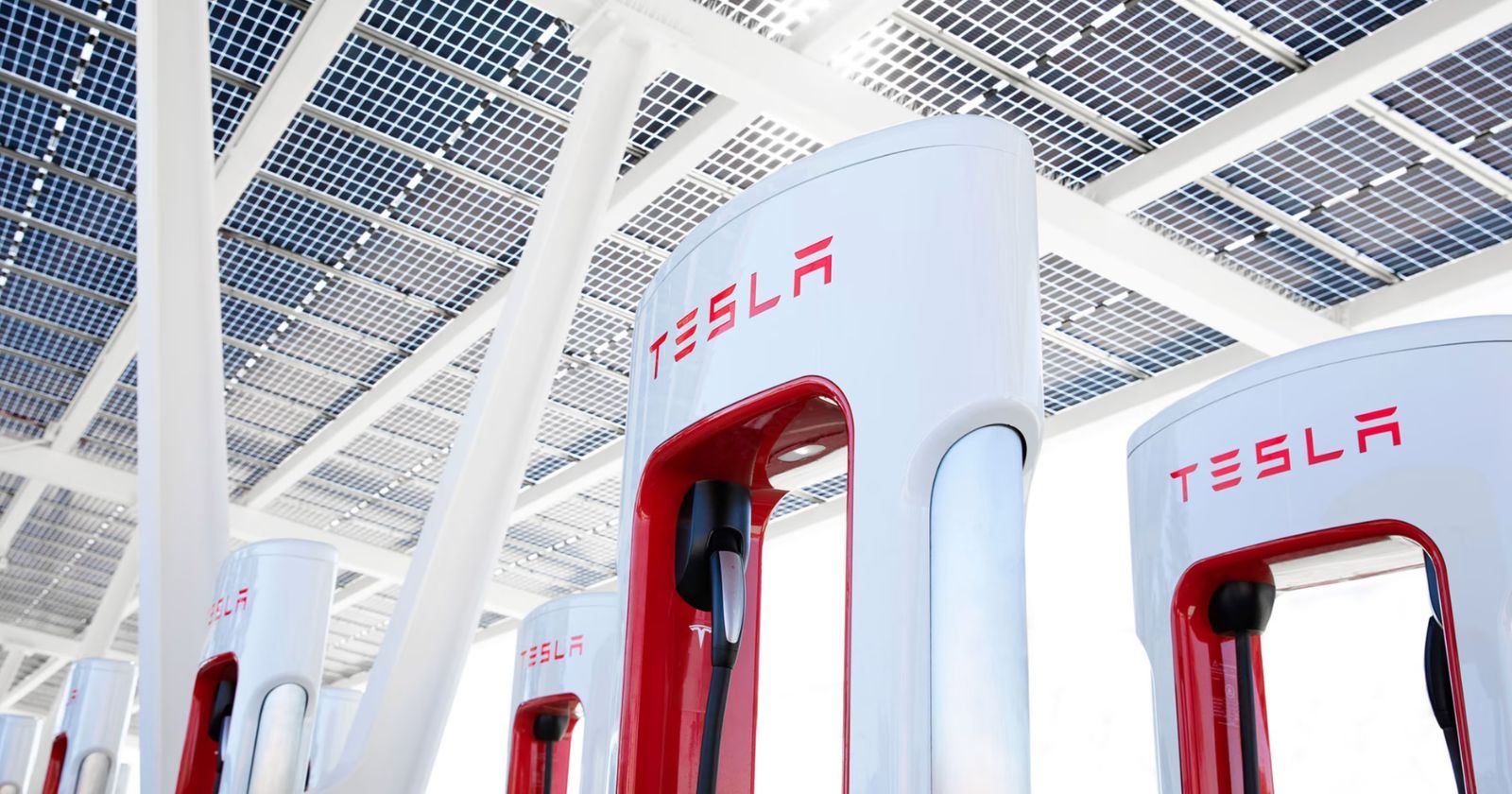
The new unboxed manufacturing system is critical for Tesla to compete with Chinese EV startups.
Share Post
The new unboxed manufacturing system is critical for Tesla to compete with Chinese EV startups.
In its quest to produce an affordable $25,000 electric vehicle (EV), Tesla is set to overhaul the century-old assembly line pioneered by Henry Ford. The company, known for pushing the boundaries of modern automobile manufacturing and championing sustainable propulsion, faces stiff competition from Chinese manufacturers who benefit from government support and a localised supply chain. To address this challenge, Tesla has introduced the "unboxed" approach, which was first revealed at its Investor Day event last year.
The unboxed approach entails building a car using a modular system, akin to Lego blocks, rather than the traditional production line where a large rectangular car moves along a conveyor belt. Under this new method, parts will be assembled simultaneously in dedicated areas and then brought together at the end. Tesla estimates that this approach could reduce manufacturing footprints by more than 40%, allowing for faster and more cost-effective factory construction. This method also bears similarities to the manufacturing process used in the consumer electronics industry.
According to Caresoft, the new Tesla Model Y, when manufactured using the unboxed parallel modular manufacturing process, will reduce costs by over 30% compared to the current manufacturing process. But this is also a car that hasn’t been envisioned for this kind of a manufacturing system, and yet there are gains to be had.
Lars Moravy, the VP of engineering at Tesla, describes the traditional method of manufacturing a car as problematic. He states that once a car is put together, only so many people can fit in it and around it to install components which slows things down. He adds that a lot of time and energy is wasted as a 5 metre long vehicle must be moved from station to station on an assembly line.
By breaking up the car into subassemblies using the unboxed method, more bodies have room to assemble components simultaneously. Tesla estimates that this approach can reduce vehicle production costs by as much as 50% and allow for the construction of vehicles in factories that are 40% smaller.
The unboxed method will also enable Tesla to incorporate advanced robots, such as the Optimus Bot, which is currently being tested at its GigaFactories, providing a greater degree of automation. The Tesla Bot could work alongside human operators, enhancing efficiency and safety, and can be redeployed across different modules and programmed accordingly – a flexibility that may not be possible with human workers. Additionally, Tesla could further optimise its supply chain and incorporate more specialised components.
Renault Group Appoints François Provost as CEO and Director: Strategic Shift for Global Growth
Ameya Naik 30 Jul, 2025, 5:13 PM IST
Tata Motors to Acquire Iveco Group in All-Cash Deal, Eyes Global Leadership in Commercial Vehicles
Ameya Naik 30 Jul, 2025, 5:08 PM IST
BSA Bantam 350: Key Highlights
Sutanu Guha 30 Jul, 2025, 1:18 PM IST
Mahindra Posts 24% Jump in Q1 Profit, Clocks Record SUV Market Share at 27.3%
Ameya Naik 30 Jul, 2025, 12:18 PM IST
Snapdragon For India Auto Day: Safe And Smart Automotive Strategy, India As Global Innovation Hub, More
Krishna SinhaChaudhury 30 Jul, 2025, 12:02 PM IST
Looking for a new car?
We promise the best car deals and earliest delivery!